Demystifying Dynamic Testing in Mold Verification of Shaoyi
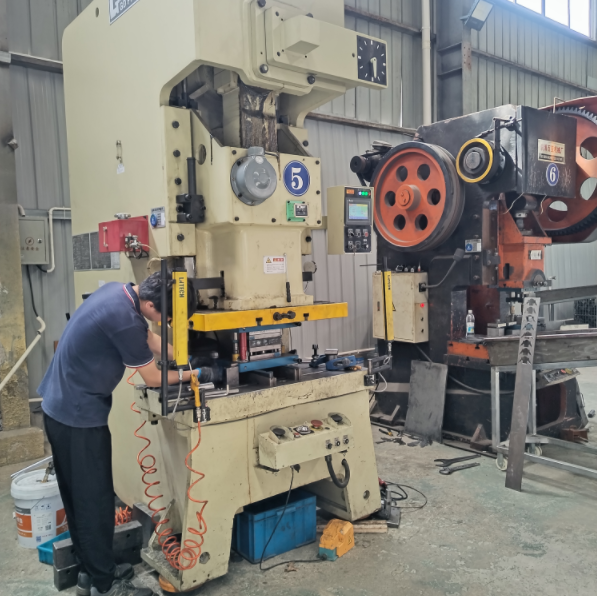
Introduction:
Dynamic acceptance mainly focuses on the qualification level of stamped parts.In the fast-paced world of manufacturing, ensuring the quality and precision of molds is paramount. One crucial aspect of this quality assurance process is dynamic mold testing, a sophisticated technique that plays a pivotal role in validating the performance and reliability of molds. In this blog, we will delve into the intricacies of dynamic mold testing, exploring what it is, its significance in the manufacturing landscape, and the benefits it offers to industries striving for excellence.
Understanding Dynamic Mold Testing:(shaoyi – shaoyi (nbshaoyi.com)
Dynamic mold testing, also known as dynamic mold validation or dynamic mold verification, is a comprehensive approach to assess the performance of molds under real-world conditions. Unlike static testing, which evaluates molds in a stationary state, dynamic testing involves subjecting molds to dynamic forces, vibrations, and movements that simulate the actual working environment they will encounter during production.
The Significance of Dynamic Testing:
Dynamic mold testing is of paramount importance because it mimics the dynamic conditions molds will face during the manufacturing process. This includes factors such as injection pressure, cooling cycles, and ejection forces. By subjecting molds to these dynamic forces, manufacturers can uncover potential issues that may not be evident during static testing alone.
Key Components of Dynamic Mold Testing:
a. Injection Pressure Analysis:
Dynamic testing evaluates how molds respond to varying injection pressures, helping manufacturers identify potential weak points or stress concentrations.
b. Vibration and Resonance Testing:
Assessing how molds handle vibrations and resonance is crucial, especially in high-speed production environments. Dynamic testing helps identify any resonance-related issues that may affect mold performance.
c. Cooling Cycle Simulation:
Dynamic mold testing replicates the cooling cycles molds undergo during production. This ensures that molds can effectively dissipate heat and maintain dimensional stability.
d. Ejection Force Evaluation:
Understanding how molds withstand ejection forces is critical for preventing premature wear and tear. Dynamic testing allows manufacturers to assess the durability of mold components under realistic conditions.
Benefits of Dynamic Mold Testing:
a. Enhanced Quality Assurance:
By simulating real-world production conditions, dynamic mold testing provides a more comprehensive assessment of mold performance, leading to higher quality assurance standards.
b. Early Issue Detection:
Dynamic testing helps identify potential issues early in the manufacturing process, allowing for timely adjustments and preventing costly defects in the final product.
c. Optimized Mold Design:
Insights gained from dynamic testing enable manufacturers to optimize mold designs, ensuring they can withstand the dynamic forces associated with high-volume production.
d. Increased Production Efficiency:
With molds validated under realistic conditions, manufacturers can enhance production efficiency by minimizing downtime and reducing the risk of mold failures during operation.
Challenges and Considerations:
a. Complexity of Simulation:
Dynamic mold testing involves complex simulations that need to accurately replicate real-world conditions. Achieving this level of accuracy requires advanced testing equipment and expertise.
b. Resource Investment:
Implementing dynamic testing may require additional resources, including specialized testing equipment and skilled personnel. However, the long-term benefits often outweigh the initial investment.
The Future of Dynamic Mold Testing:
As manufacturing technologies continue to advance, the future of dynamic mold testing holds exciting possibilities. Innovations in simulation technologies, artificial intelligence, and data analytics are expected to further refine and streamline dynamic testing processes, providing manufacturers with even greater insights into mold performance.
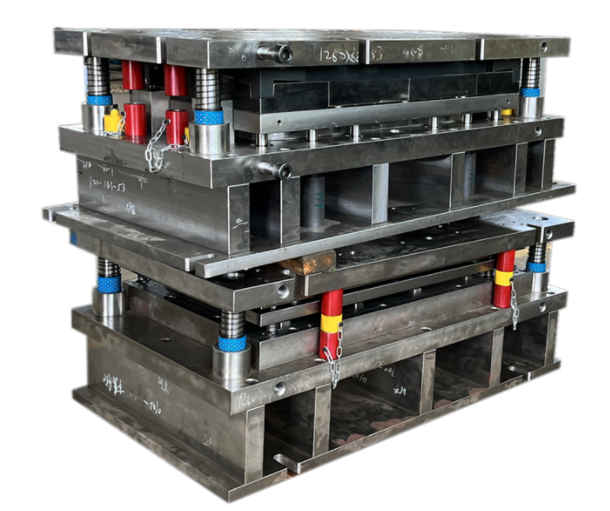
Conclusion:
Dynamic mold testing stands as a critical pillar in the quality assurance framework of modern manufacturing. By subjecting molds to real-world conditions, manufacturers can ensure the reliability, durability, and efficiency of molds in high-speed production environments. As technology continues to evolve, dynamic mold testing will play an increasingly pivotal role in the quest for manufacturing excellence, enabling industries to push the boundaries of innovation and set new standards for quality and precision in mold verification.
Interested in learning more about Shaoyi’s innovative solutions in automotive stamping mold ? Let’s Create Success Together! Contact us (contact (nbshaoyi.com)to start shaping a brighter business future.