In-Depth Understanding of the Die Casting Process: From Design to Production
Introduction:
Die casting is a versatile manufacturing process that involves forcing molten metal into a mold cavity under high pressure. This technique is widely used to produce complex and precise metal parts with high dimensional accuracy and excellent surface finish. At Shaoyi, a precision machining factory specializing in custom die-casting of automotive parts, we are equipped with state-of-the-art automation and 100% inspection capabilities. This blog will provide an in-depth understanding of the die casting process, from initial design to final production.
Overview of Die Casting
Die casting is a process where molten metal is injected into a steel mold under high pressure. The mold, known as a die, is designed to create complex shapes with high precision and repeatability. The process is ideal for producing large volumes of small to medium-sized parts with intricate details. Common metals used in die casting include aluminum, magnesium, and zinc alloys.
Design Phase
1. Conceptualization
– The process begins with the conceptualization of the part. This involves understanding the requirements, functionality, and constraints of the part.
– At Shaoyi, our engineers collaborate closely with clients to ensure that all specifications and performance criteria are met.
2. Material Selection
– Choosing the right material is crucial for the success of the die casting process. Factors such as strength, weight, thermal properties, and cost must be considered.
– Aluminum alloys are preferred for automotive applications due to their lightweight and excellent mechanical properties.
3. CAD Modeling
– Once the material is selected, a detailed CAD model of the part is created. This model serves as the blueprint for the die design.
– Advanced CAD software allows our engineers to simulate the casting process and identify potential issues before production begins.
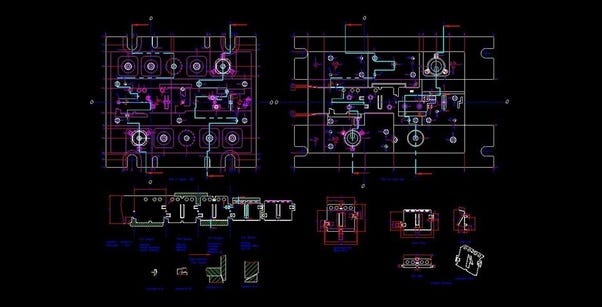
4. Prototype Development
– Prototypes are often created using 3D printing or other rapid prototyping methods. This helps in validating the design and making necessary adjustments.
– Prototyping at Shaoyi ensures that the final part meets all design and functional requirements.
Mold Design and Manufacturing
1. Mold Design
– The next step is designing the mold, which consists of two halves: the cover die and the ejector die. The mold must withstand high temperatures and pressures.
– Key features such as gates, runners, and vents are designed to facilitate the flow of molten metal and the release of gases.
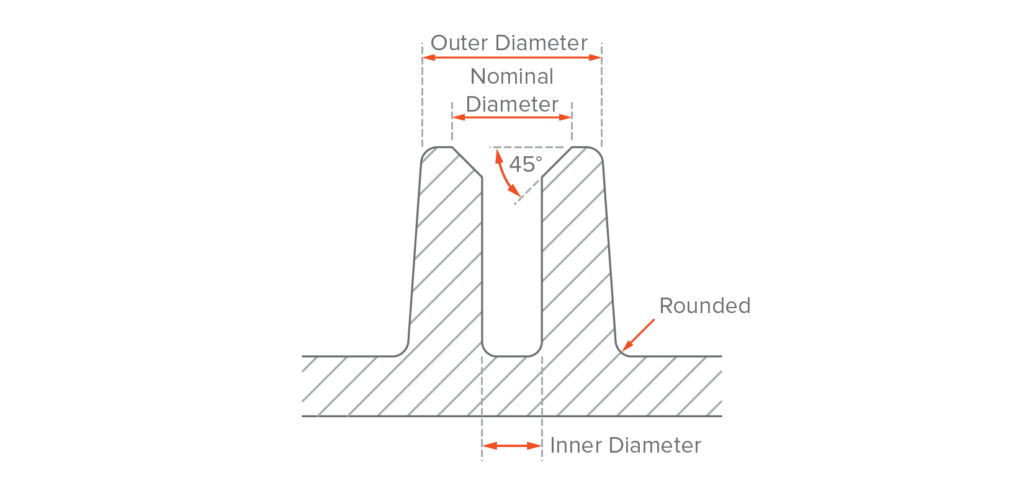
2. Mold Manufacturing
– High-quality tool steel is used to manufacture the mold. Precision machining techniques such as CNC milling and EDM (Electrical Discharge Machining) are employed.
– At Shaoyi, our advanced machining capabilities ensure that molds are produced with the highest accuracy and durability.
3. Mold Testing
– Before full-scale production, the mold undergoes rigorous testing to identify any defects or areas for improvement. This includes trial runs and adjustments.
– Our 100% inspection process guarantees that the mold meets all specifications and is ready for production.
Production Phase
1. Melting and Injection
– The selected metal is melted in a furnace and maintained at a precise temperature. The molten metal is then injected into the mold cavity under high pressure.
– At Shaoyi, our automated systems ensure consistent and precise control of the melting and injection process.
2. Solidification and Cooling
– Once the molten metal fills the mold cavity, it begins to cool and solidify. The cooling rate must be controlled to prevent defects such as porosity and shrinkage.
– Cooling systems integrated into the mold help in maintaining the desired cooling rate and ensuring uniform solidification.
3. Ejection and Trimming
– After solidification, the mold is opened, and the cast part is ejected. Trimming is performed to remove excess material and achieve the final dimensions.
– Automated trimming and finishing equipment at Shaoyi ensures high efficiency and precision in the production process.
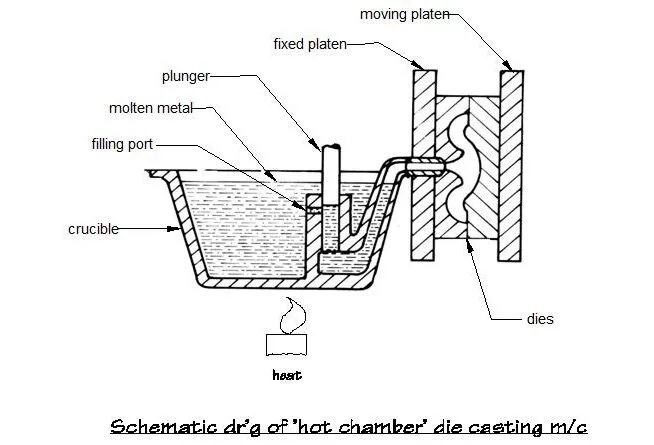
Post-Processing and Inspection
1. Surface Treatment
– Post-processing treatments such as shot blasting, machining, and coating are applied to enhance the surface quality and performance of the cast parts.
– Our state-of-the-art surface treatment facilities ensure that each part meets the highest standards of quality and durability.
2. Quality Inspection
– Every part undergoes a comprehensive inspection process to verify its dimensional accuracy, mechanical properties, and surface finish.
– Shaoyi’s 100% inspection protocol utilizes advanced inspection tools such as CMM (Coordinate Measuring Machines) and X-ray testing.
3. Assembly and Packaging
– For parts requiring assembly, precise and efficient assembly processes are employed. The final products are then carefully packaged for shipping.
– Our packaging solutions ensure that parts are protected during transportation and reach our clients in perfect condition.
Shaoyi’s Commitment to Quality and Innovation
At Shaoyi, we are committed to pushing the boundaries of die casting technology. Our investment in advanced automation and inspection systems ensures that we deliver high-quality, custom automotive parts that meet the exacting standards of our clients. We continuously innovate to improve our processes and stay at the forefront of the industry.

Sustainability and Environmental Responsibility
1. Recycling and Waste Management
– Die casting is inherently sustainable due to the high recyclability of metals. Scrap metal from the casting process is collected and recycled, reducing waste and conserving resources.
– Shaoyi is dedicated to implementing efficient recycling programs and minimizing waste generation.
2. Energy Efficiency
– Our modern die casting facilities are designed to minimize energy consumption. Advanced melting and casting technologies reduce the overall energy footprint of our operations.
– Continuous efforts are made to optimize energy use and adopt renewable energy sources where possible.
3. Emission Control
– Emission control systems are in place to reduce pollutants and ensure compliance with environmental regulations. Clean fuel technologies and advanced filtration systems contribute to a greener manufacturing process.
– Shaoyi actively monitors and controls emissions to minimize our environmental impact.
Future Directions: Embracing Advanced Technologies
1. Integration of Additive Manufacturing
– Combining additive manufacturing with die casting allows for greater design flexibility and the production of complex, high-performance components.
– At Shaoyi, we explore hybrid manufacturing techniques to offer innovative solutions to our clients.
2. Implementation of Industry 4.0
– Industry 4.0 principles, such as real-time data monitoring and smart manufacturing, transform the die casting process. These technologies enhance process control and ensure consistent quality.
– Shaoyi leverages Industry 4.0 to optimize production and improve efficiency.
3. Development of New Alloys
– Ongoing research into new alloys aims to enhance the properties of die-cast components. High-entropy alloys and superalloys offer superior performance in extreme environments.
– Our R&D team collaborates with industry and academic partners to develop cutting-edge materials.
Conclusion:
Die casting is a complex and highly technical process that requires expertise at every stage, from design to production. At Shaoyi, we are dedicated to delivering the highest quality custom die-cast automotive parts through our advanced automation and rigorous inspection processes. As we continue to innovate and embrace new technologies, we remain committed to sustainability and environmental responsibility. By understanding and mastering each aspect of the die casting process, we ensure that our clients receive products that meet their exact specifications and performance requirements.
Request for Quote (RFQ) Information
If you are interested in Shaoyi’s custom die-casting services, please provide the following information in your RFQ:
1. Project Specifications
– Detailed drawings and technical specifications of the required parts.
– Material requirements and desired tolerances.
2. Quantity and Timeline
– Estimated quantity of parts needed.
– Preferred delivery schedule and deadlines.
3. Quality and Inspection Requirements
– Specific quality standards and inspection criteria.
– Any additional testing or certification requirements.
4. Packaging and Shipping
– Packaging preferences to ensure safe transportation.
– Shipping instructions and destination details.
5. Contact Information
– Your company’s contact details, including the primary point of contact.
– Any additional notes or special instructions for your project.
FAQ
1. What makes Shaoyi’s die casting services unique?
– Shaoyi offers state-of-the-art automation,100% inspection, and custom automotive parts production. Our advanced technology ensures precision and quality.
2. How does Shaoyi ensure the quality of its die-cast products?
– We utilize advanced simulation, modeling software, and a 100% inspection process. This guarantees each part meets our stringent quality standards.
3. What industries does Shaoyi serve?
– Shaoyi specializes in automotive parts but also serves aerospace, consumer electronics, medical devices, and renewable energy sectors.
By providing detailed information and understanding the complete die casting process, we aim to establish Shaoyi as a leader in precision die-casting solutions. Our commitment to quality, innovation, and sustainability ensures that we deliver exceptional value to our clients.