Auto Welding Assembly
Free CAE Analysis, Rapid Modeling, 24-Hour Quotation. Plus, Complimentary Welding Testing Support!
UPLOAD A PART >>
SAMPLE DESIGN ANALYSIS >>
Certificate
IATF TS16949:2016/Critical to Quality
55 million
Parts finished each month
15+
R&D Engineer
20+
Steel & Aluminum
Welding Process
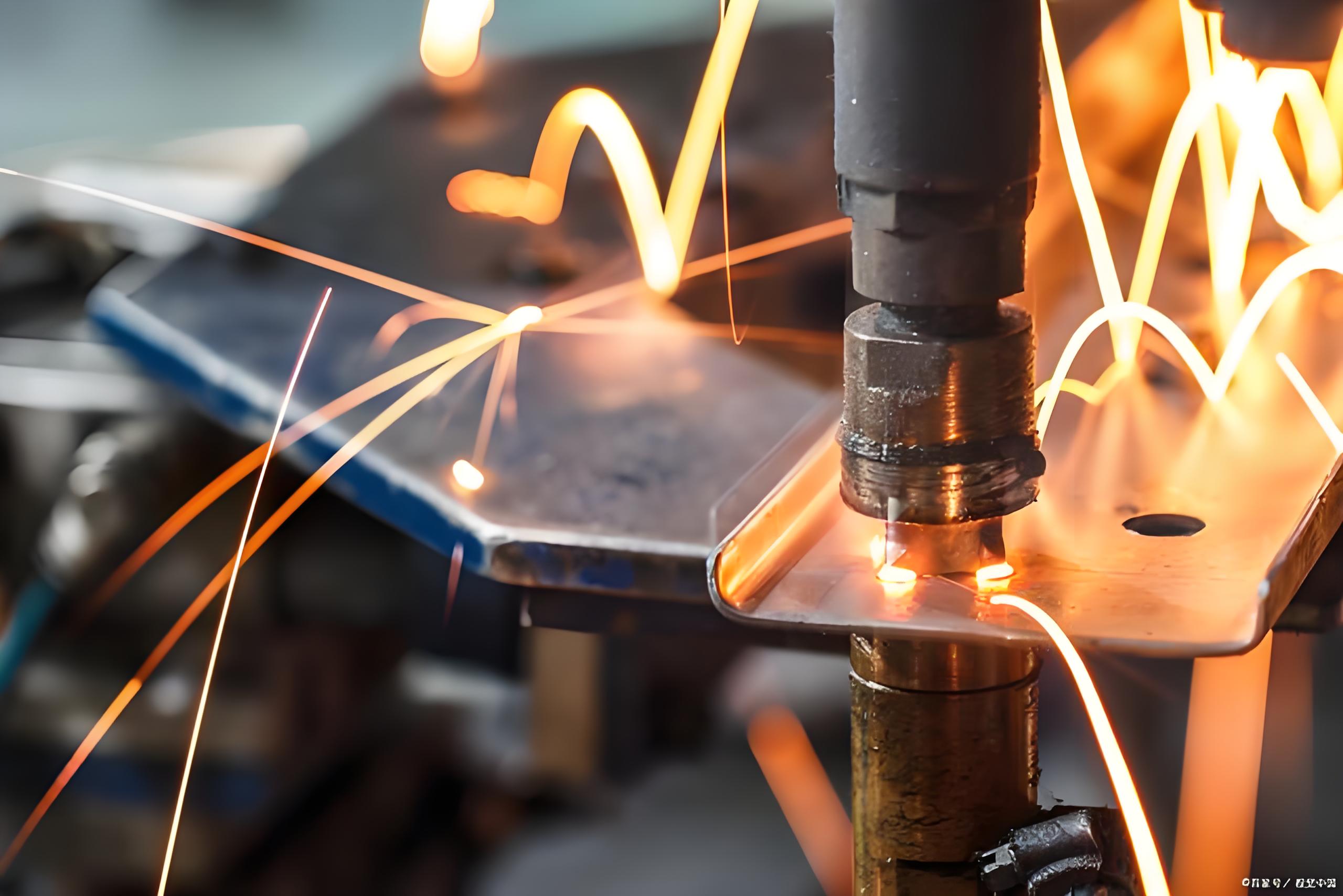
RESISTANCE WELDING
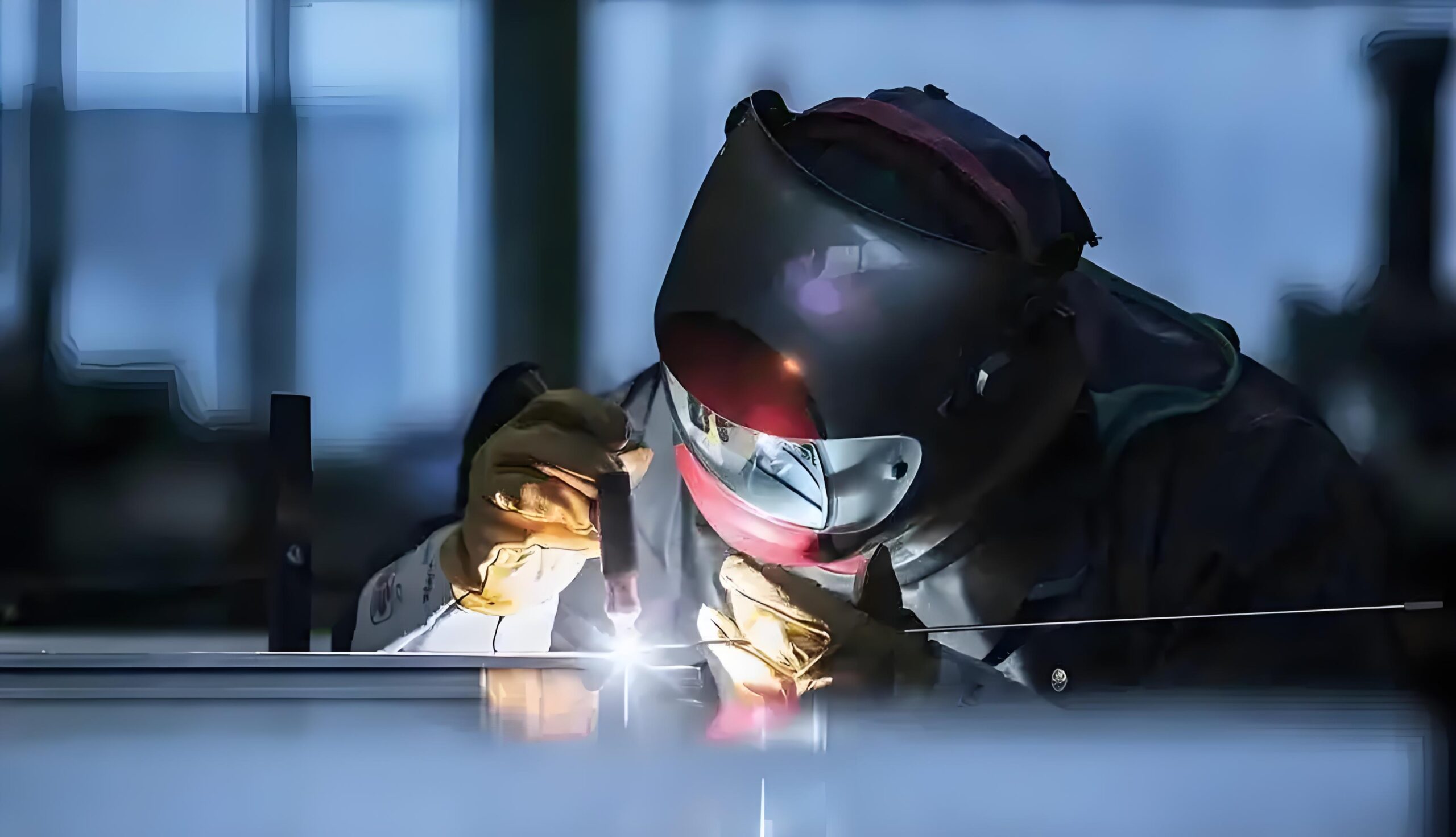
TigWelding
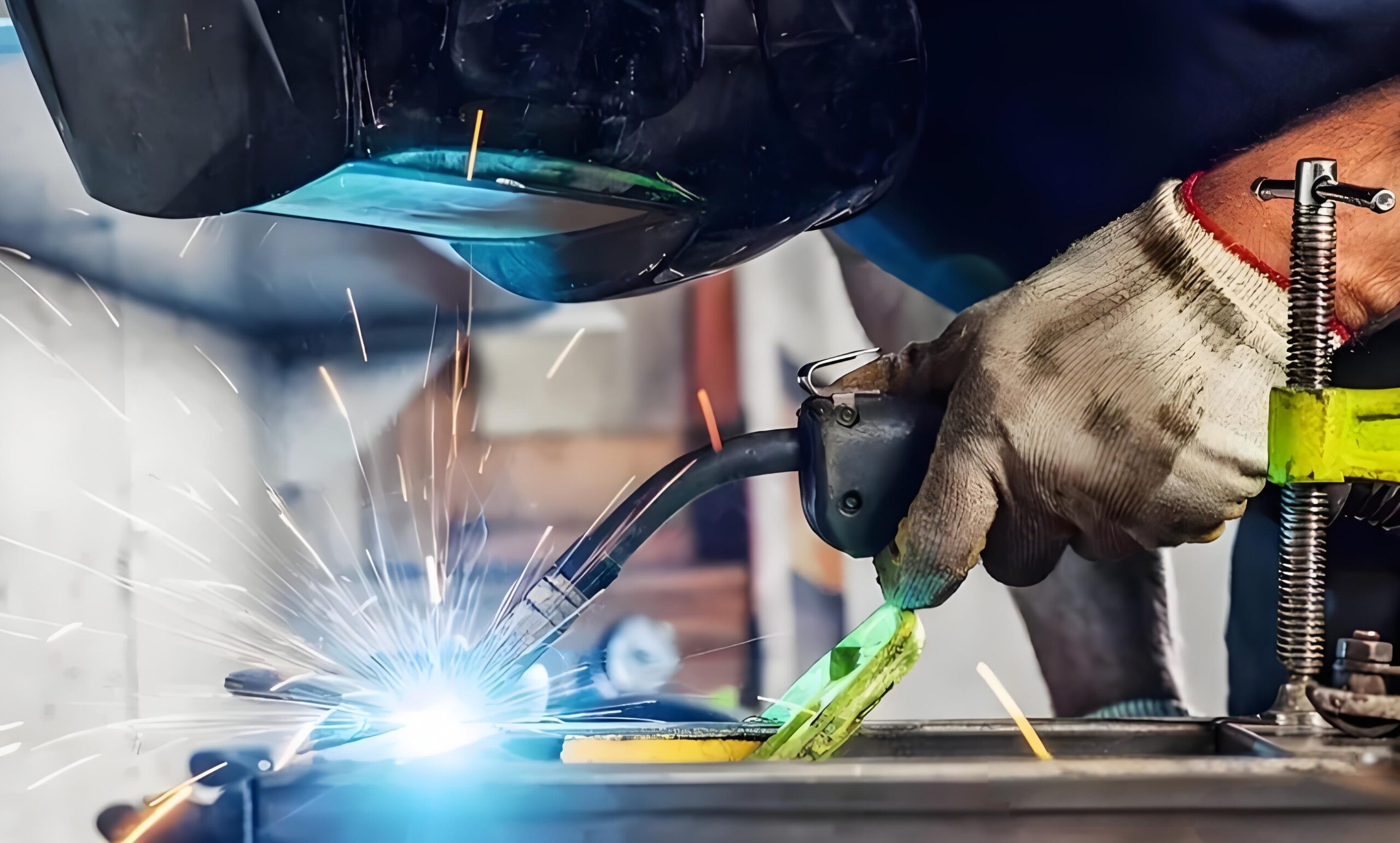
Gas Shielded Arc Welding
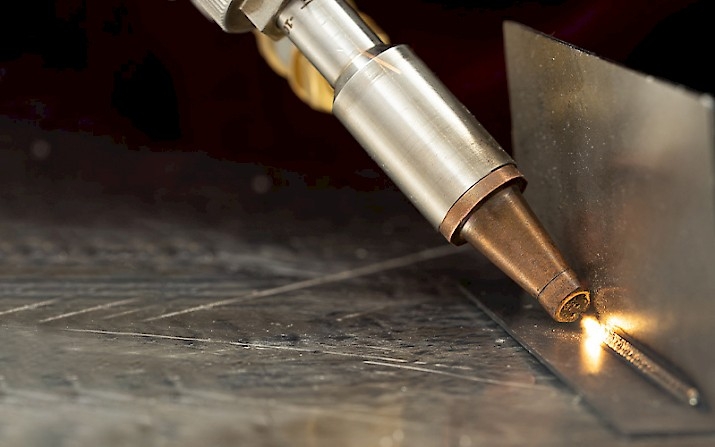
Laser Welding
Metal Machining For Automotive
Project Management Process
Requirement input (drawing. standard technical requirement)
1
Quotation
2
Starting
3
Products planning (CAE analyse,prem-inary planning)
4
Products design (sample –softmold -DV)
5
Products design (sample –softmold -DV)
6
Product validation
7
Sample(PV-PPAP)
8
2TP
9
OTS
10
Production Advantages
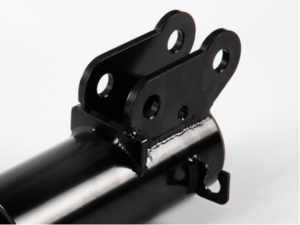
High Precision and Consistency
We utilize state-of-the-art automated welding equipment and technology to ensure the precision and consistency of every weld. Our welding processes minimize human error, guaranteeing high-quality and strong weld joints, suitable for complex designs and demanding projects.
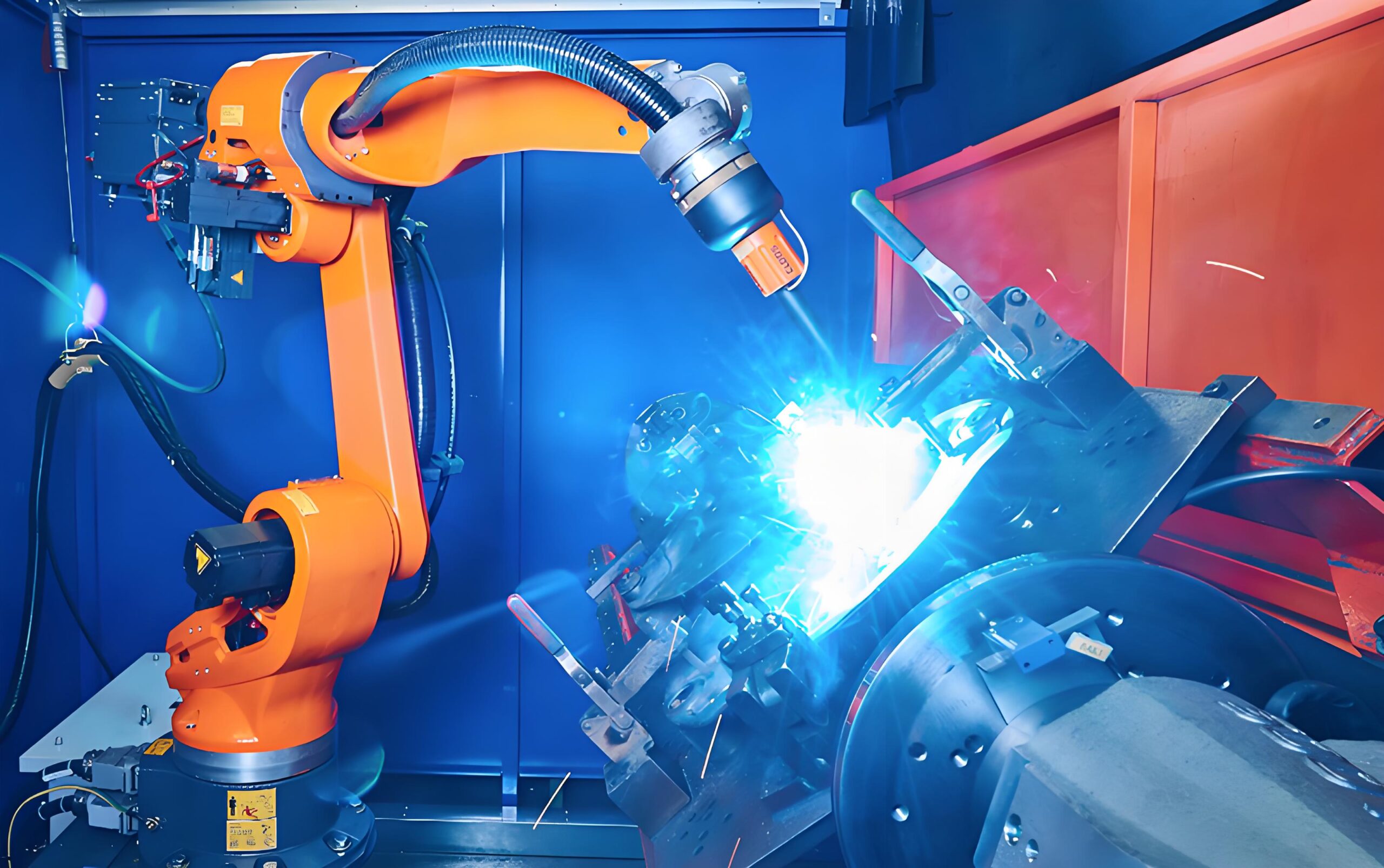
Efficient Production and Quick Turnaround
Automated welding technology significantly enhances production efficiency. Our equipment operates continuously without frequent stops, greatly reducing production cycles. We commit to quick turnaround times, ensuring your projects are completed on schedule.
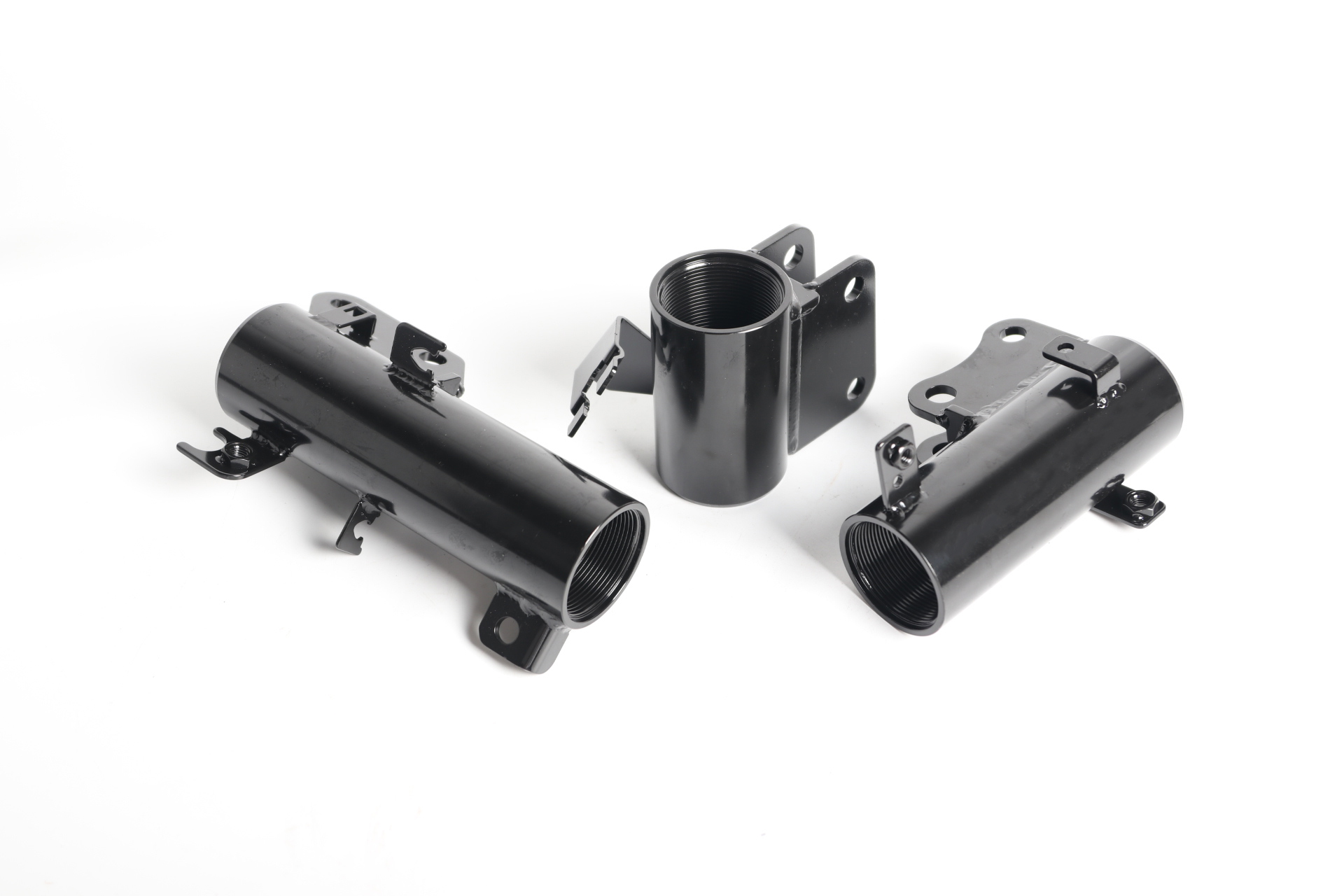
Versatility in Materials and Processes
We are capable of welding various metals, including stainless steel, aluminum, and carbon steel. Whether it's MIG welding or TIG welding, we provide the best welding solutions to meet the needs of different materials and projects.
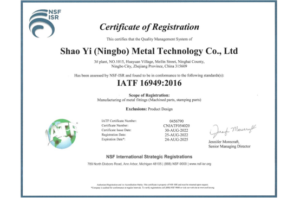
Stringent Quality Control
Our welding team is AWS certified and adheres to the IATF 16949 Quality Management System. We conduct rigorous quality inspections for every welding project to ensure defect-free welds and deliver high-quality products that meet our clients' stringent requirements.
Production Workshop
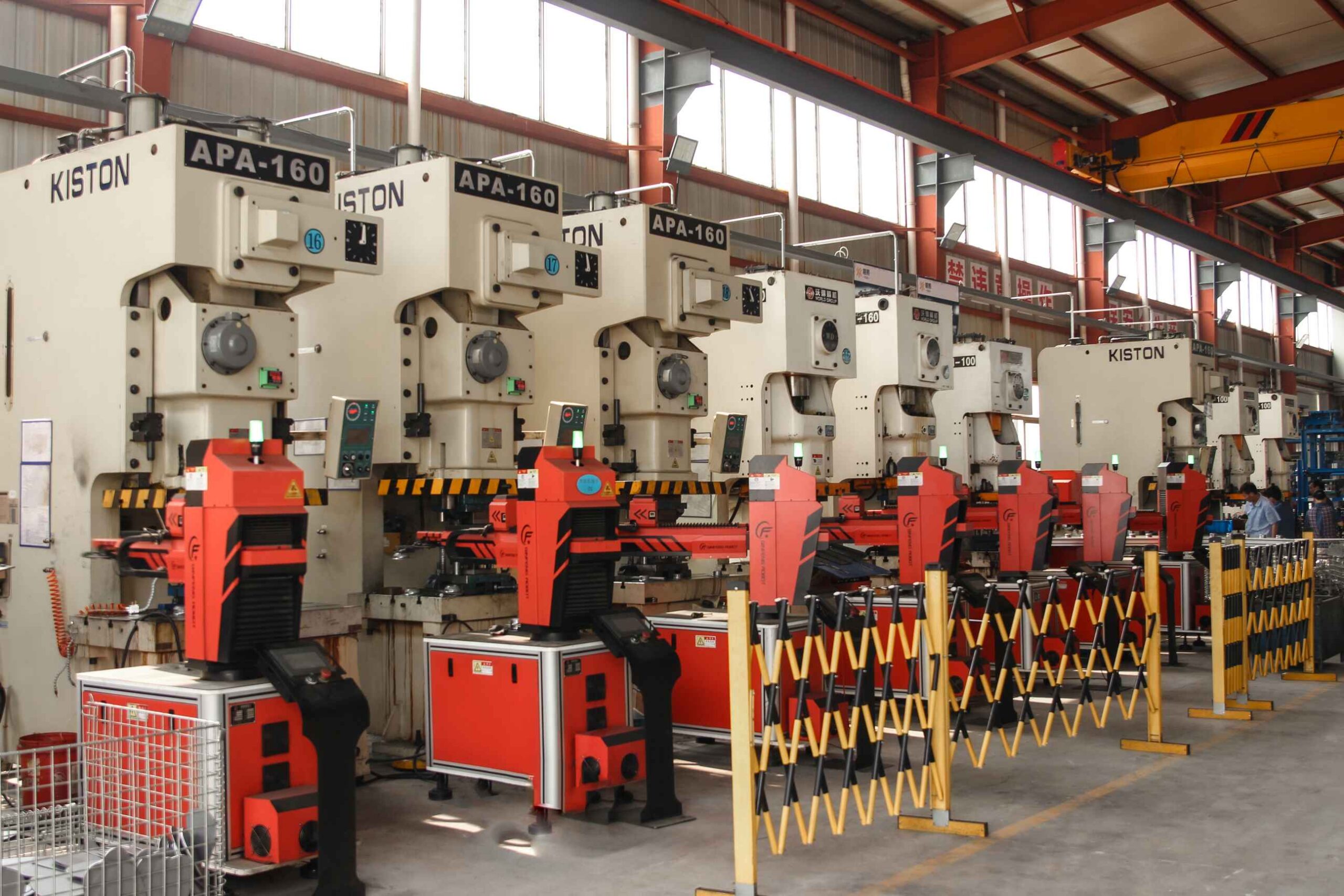
Automated Stamping Production Line
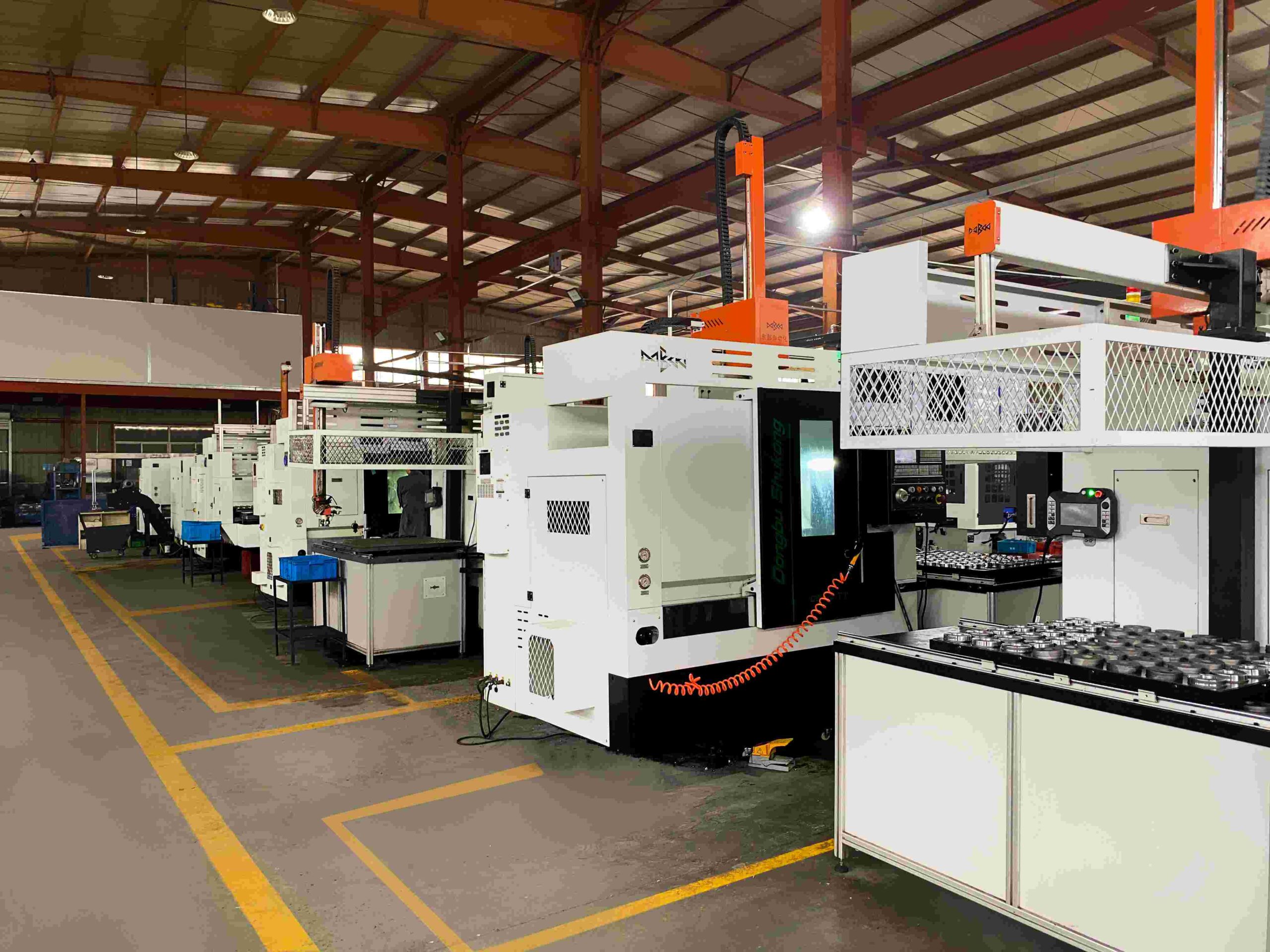
CNC Workshop
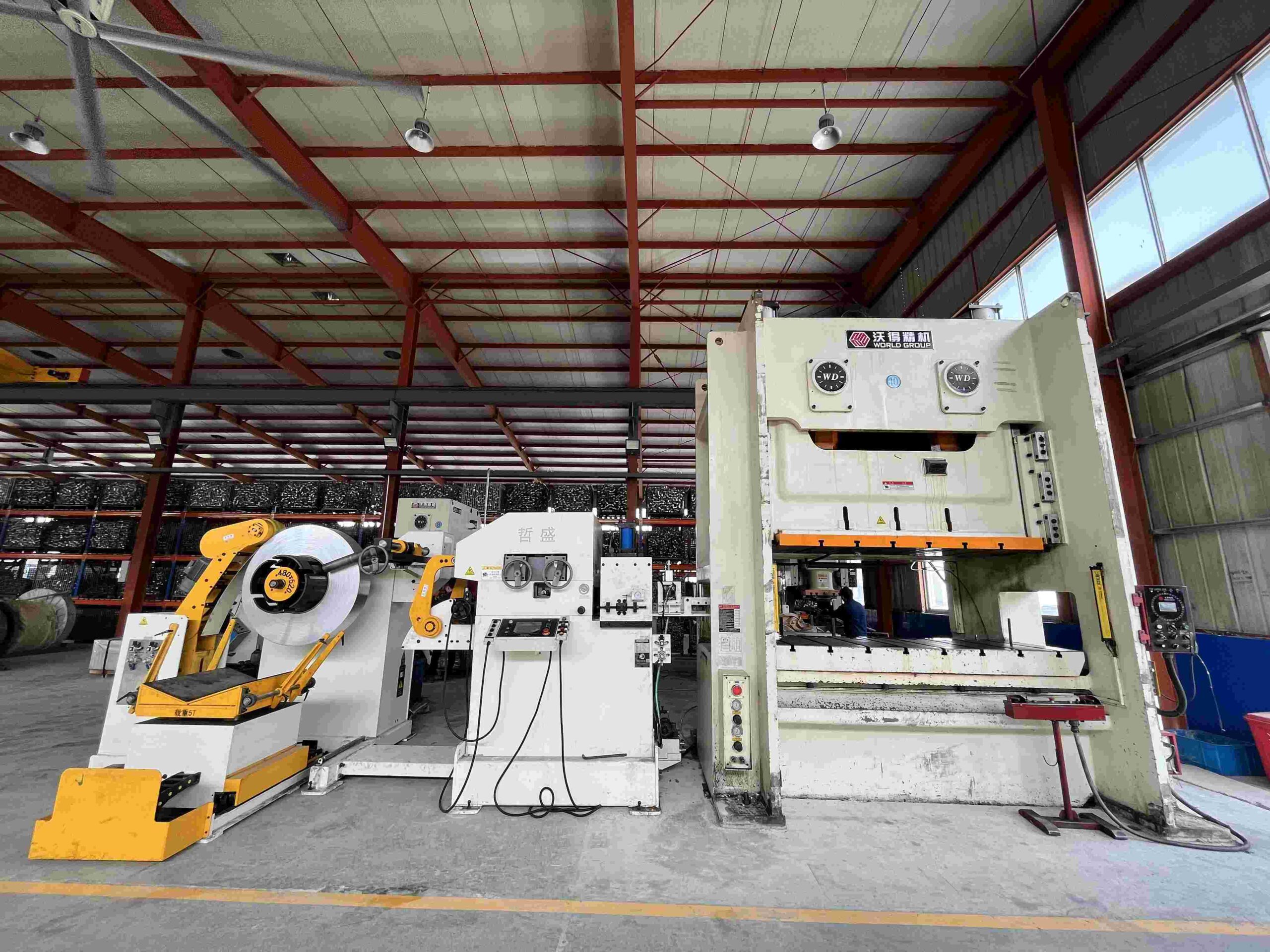
Heavy-Duty Stamping Press
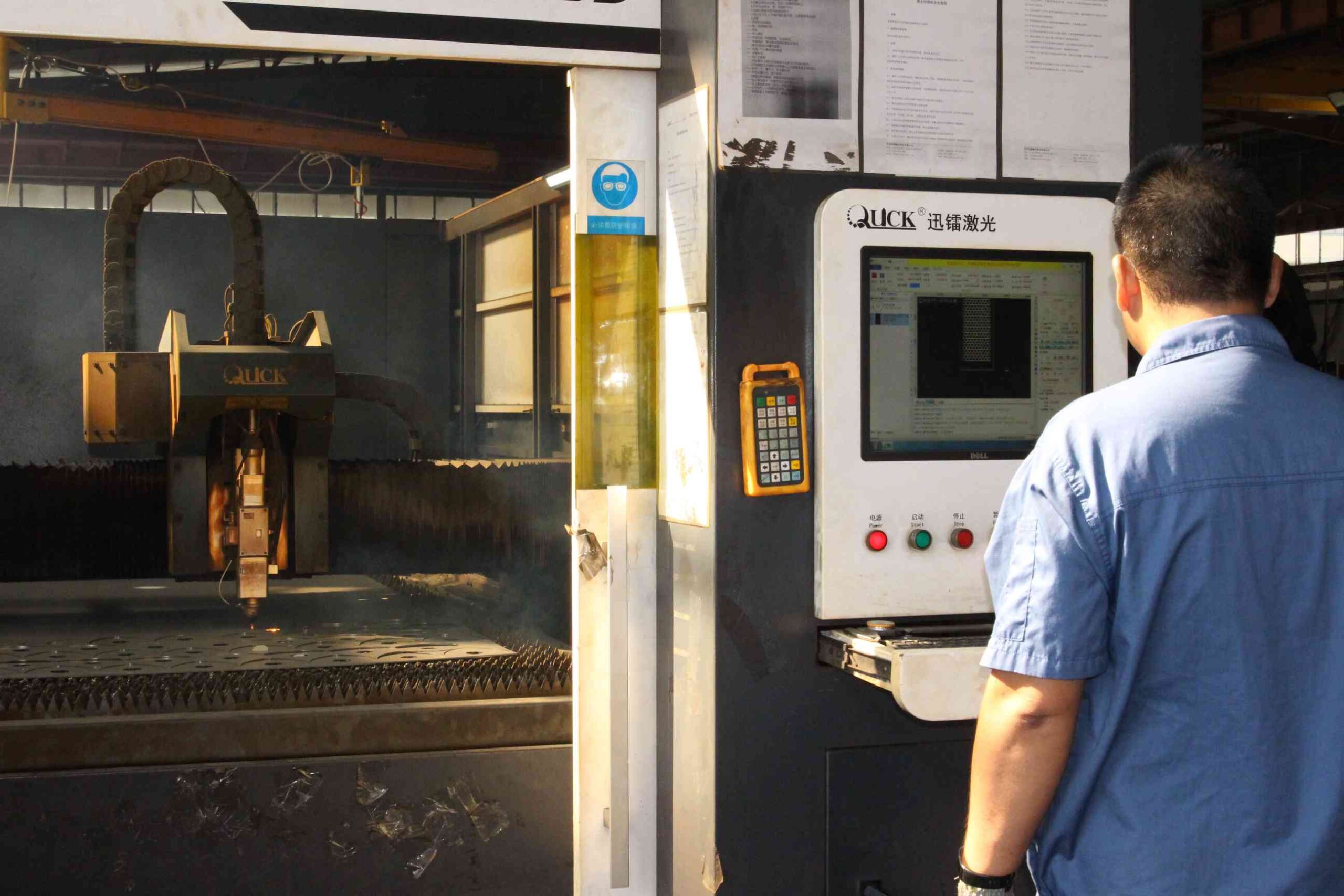
Laser Cutting
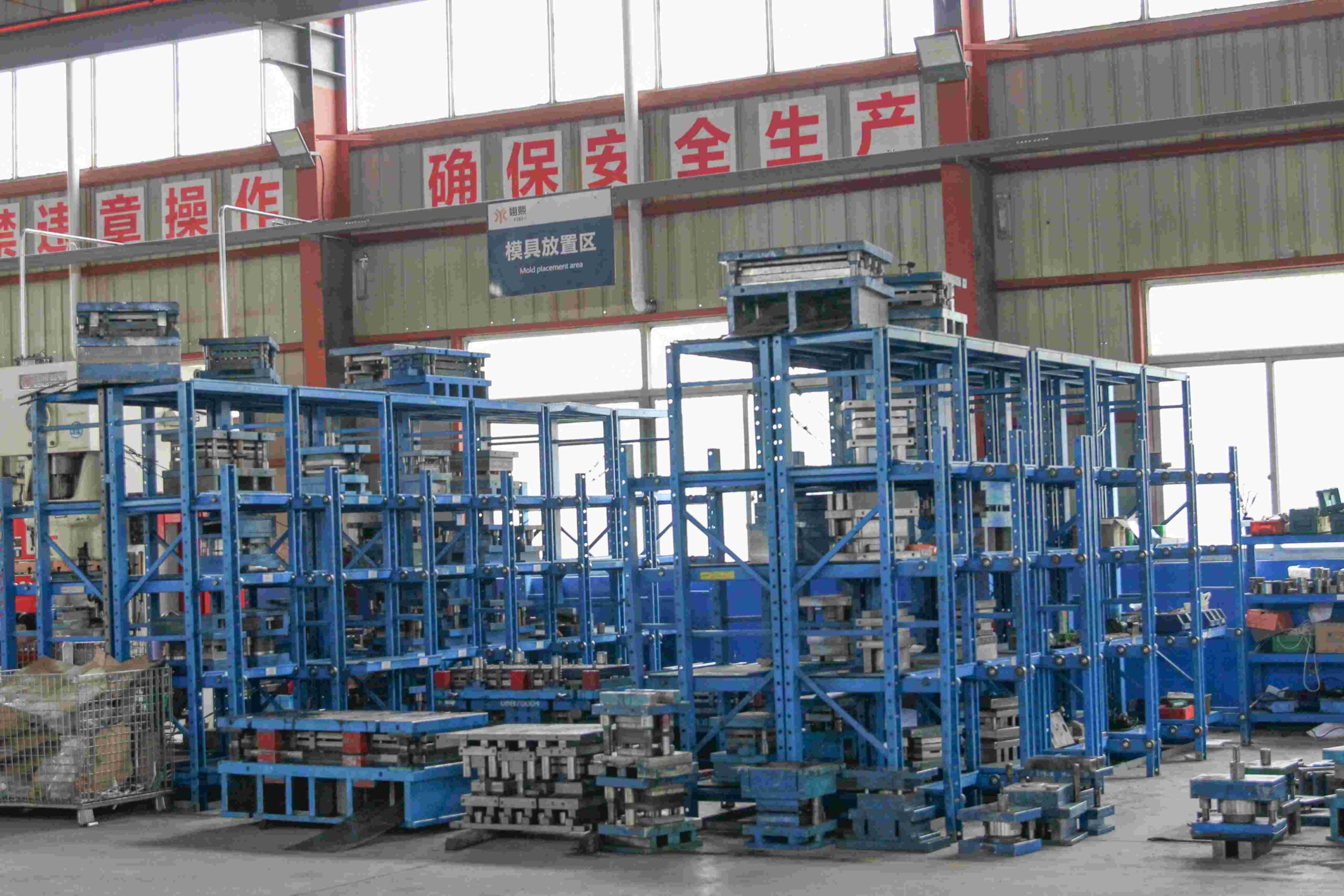
Mold Area
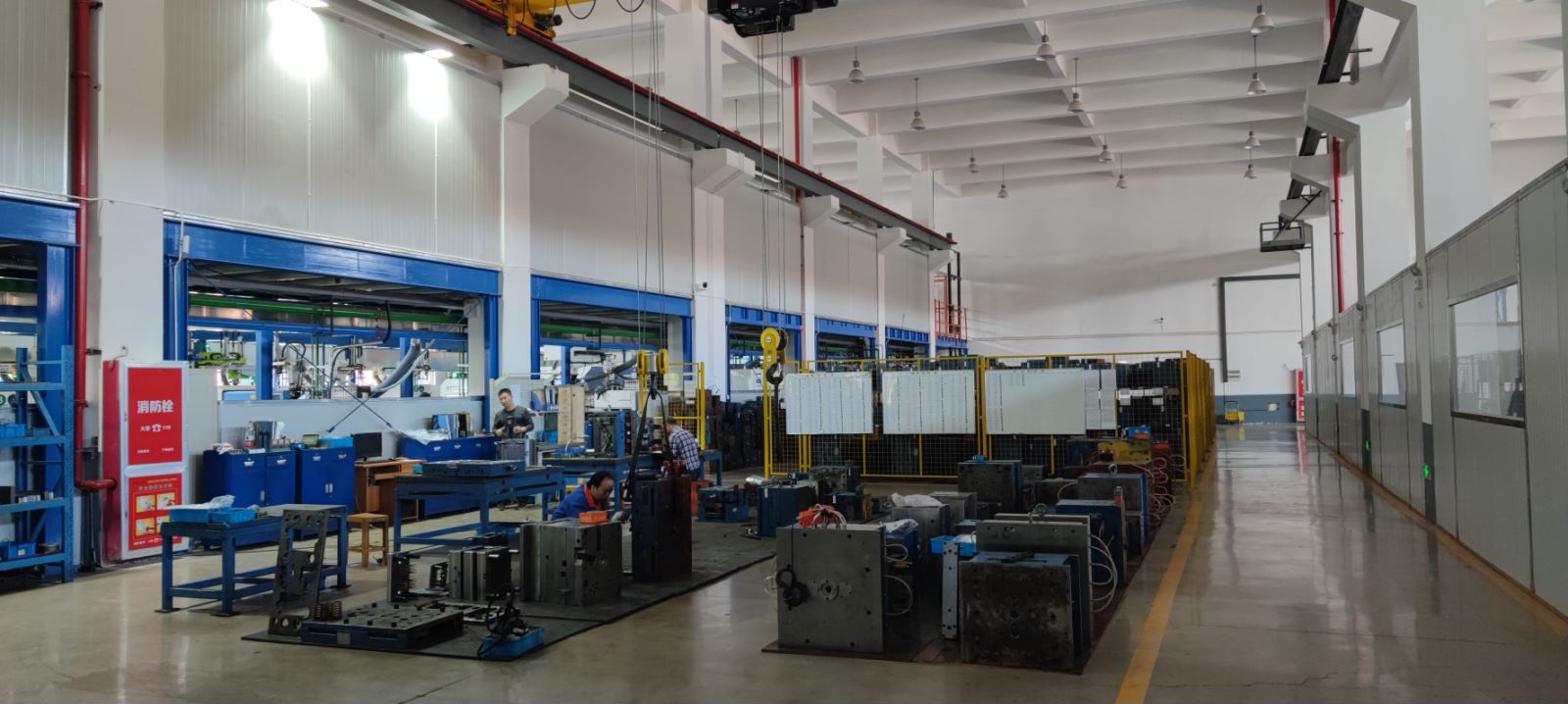
Mould Production Area
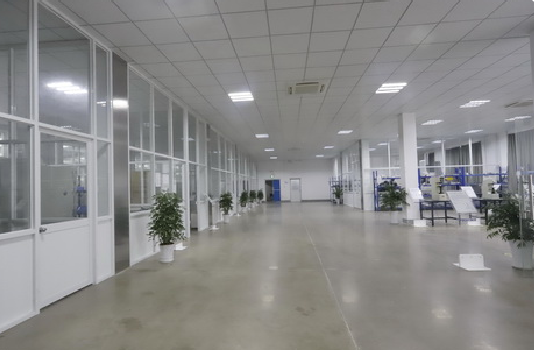
Quality Control Laboratory
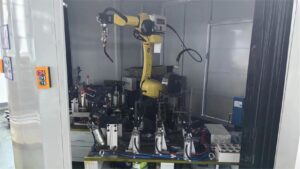
Welding Workshop
Inspection Personnel
Eight Core Processes Only In Pursuit Of Achieving Sub-2000 Dppm Efforts
Standardized,process-oriented refined production standards efforts to provide you with up to 99.8%qualified string of precision parts
Processing Capabilities
Processing Capabilities | Remark | ||
---|---|---|---|
Stamping
Maximum Part Size |
Maximum coil material width: 600mm Maximum thickness (T): 6.0mm |
Stamping Maximum Part Size | The three-in-one feeding machine, paired with a 315-ton punch, imposes a limitation on material thickness, restricting it to within 6.0mm |
Stamping Minimum Part Size | Minimum width of the coil material is 300mm Minimum thickness (T): 1.0mm |
Stamping Minimum Part Size | The 160T punch, equipped with an older-style feeder, requires a material thickness of no less than 1.0mm |
Stamped Product Tolerances | Punching tolerance:0.05mm | ||
Resistance Welding Strength | Pull-off force experiment:25KN | ||
Electrophoresis | Film thickness: 15-35um Salt spray test: 720h without red rust |
||
Dacromet | Film thickness: 8um Salt spray test: 720h without red rust |
||
Galvanization | Film thickness: 8-15um Salt spray test: 240h without red rust |
||
Galvanized nickel | Film thickness: 8-15um Salt spray test: 1500h without red rust |
Surface Treatment
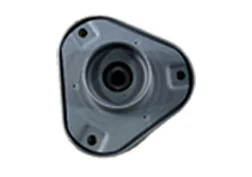
Phosphating
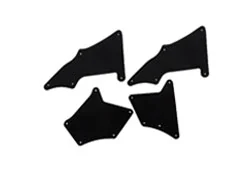
Blackening
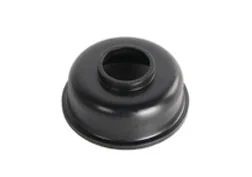
Electrophoresis
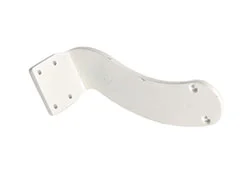
Powder Coating
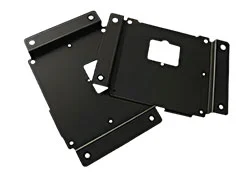
Baking Pain
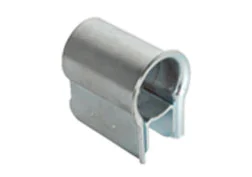
Galvanizing
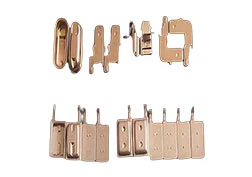
Copper Plating
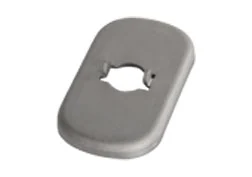
Galvanized Nickel Alloy
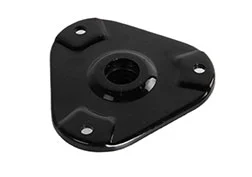
Spray Painting
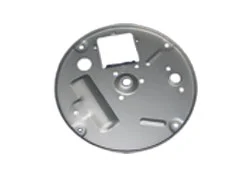
Dacromet Coating
Our Manufacturing Services
Focus on chassis welded assemblies, shock-absorbing welded assemblies, chassis stamping, and machining parts.
Frequently Asked Questions
How many years of experience do we have in the processing of automotive components? Our products cover suspension,shock absorption, and other systems in automobiles, providing services to global brands
After receiving detailed information(your 2D/3D drawings), we will quote you within 12 hours. If the quote is delayed by some reasons, we will notify you.
Contact Us
Complete control over products allows us to ensure our customers receive the best quality prices and
service
INQUIRY FORM
After years of devepopment, the company's welding technology mainnly includes gas shielded welding,
arc welding, laser welding and kinds of welding technologies, combined with automatic assemble
lines, through Ultrasonic Testing (UT), Radiographic Testing(RT), Magnetic particle Testing(MT)
Penetrant Testing(PT), Eddy Current Testing(ET), Pull-off force of testing, to achieve high
capacity, high quality and safer welding assemblies, we could supply CAE, MOLDING and 24-hour quick
quotation to provide customers with better service for chassis stamping parts and maching parts.
- Various automotive accessories
- Over 12 years of experience in mechanical processing
- Achieve strict precision machining and tolerances
- Consistency between quality and process
- Can achieve customized services
- On time delivery